© © Philippe SAMYN and PARTNERS
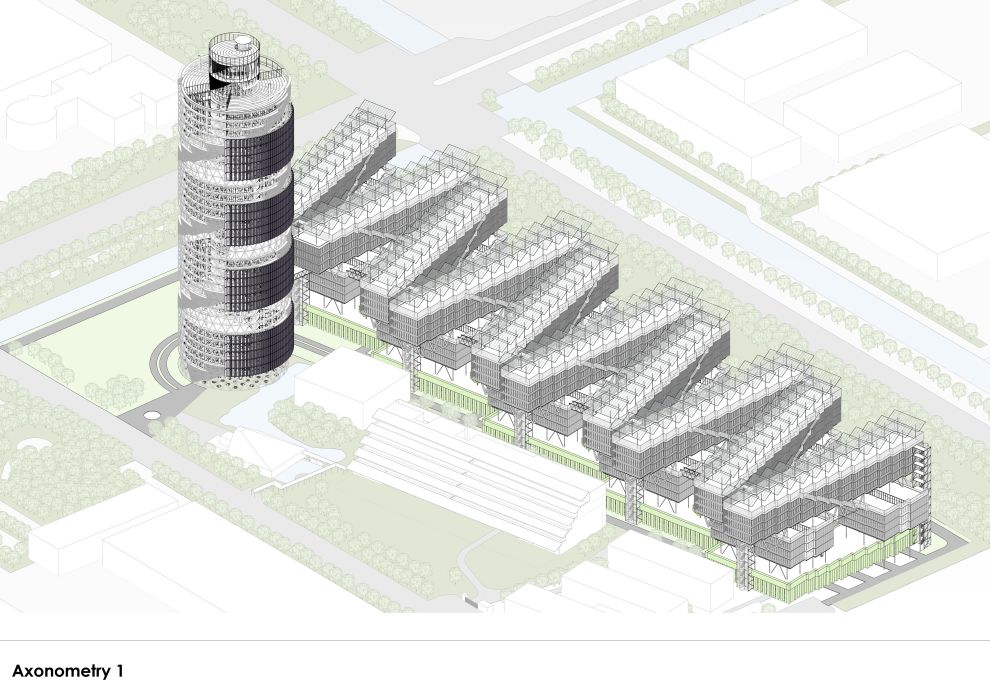
664-2 POSITEC CAMPUS – FEASIBILITY STUDY : SECOND MASTER PLAN
Suzhou (China) 31°17’27,8’’N/120°45’32,9’’E Buildings: 106,000 sqm; services and parking: 35,000 sqm; 2021- 2022; (01/664-1).
• Master plan
The nearly rectangular Positec terrain at Suzhou is bordered South by a main avenue, West and North by public gardens, East by industrial buildings, and faces the Positec factories. It covers a surface of about 240 m (North-South) by 450 m (East-West), of which about 360 m x 120 m is occupied by existing buildings.
Don Gao, our commissioner, appointed us in 2019 to design the “Positec Sun Machine” (01/664) leading this 2020-01-19 to a preliminary design for a 12,000 sqm porous “vertical village”, developed on 12 levels. A volumetric study for the build potential of the site led to locate the construction on its Southwest corner.
Taking profit of the Covid-19 pandemic, stopping temporarily the duties, Don Gao extended its views and asked for this preliminary study (01/664-1) to also consider the development of a research campus on the remaining terrain while doubling the height of the Sun Machine.
Potential of the site and organization of the Campus construction
This feasibility study concludes to an environmentally respectful and sustainable “multipurpose building potential” of 80,000 m² above a garden park (level 6), 6 m above a service-delivery-parking construction on the remaining existing terrain level to avoid earth movements and to provide it with natural lighting and ventilation.
The constructions are therefore organised, on a 1.35 m module, in relation with the site geometry and the existing building grid to benefit from its 1/5 and 1/6 angles.
1. The position of the Positec Sun Machine, although doubled in height, is confirmed in the South-West corner of the site (26,000 sqm)
2. Parallel to the existing buildings, two rows of respectively 5 and 6 lower campus building blocks of three levels rest on 9 m high columns above the level of the garden park (0 m). Their floors are respectively at levels 15 m, 19.5 m and 24 m, with a roof garden at level 28.5 m (44,000 sqm, main façades facing North and South).
3. Ten floating upper campus constructions, taking advantage of the 1/5 and 1/6 angles provided by the site and all the existing buildings, fan out with their main façades facing East and West, staggering 1.35 m every 8.1 m.
Their 3 floors, 9 m above the roof gardens of the lower building blocks, are at levels 37.5 m, 42 m and 46.5 m, topped by roof gardens at level 45 m (possibly with photovoltaic umbrellas at level 51 m, above the roof trees) (36,000 sqm).
Six North and five South outside vertical circulation shafts give normal access to the lower and upper constructions in relation with the garden park (level 6) and the basement service level (level +0 m = present site level).
One sole new access (for pedestrians, bikes, cars, utility – safety – security vehicles), South of the tower, provides access to the Campus, independently of the present main access.
The concept aims at a harmonious construction in phases, each one with its garden park comfortably liveable while next is in construction.
Campus construction concepts
Geometry
The constructions are characterized by:
1) 12.15 – 13.5 m floor depth with a floor-to-floor height of 4.5 m and a 0.9 – 1.2 m floor « thickness » (for structure, equipments and building physics). The structural span might be reduced to 6.075 – 6.75 m.
2) Catways 1.35 m wide, for external circulation (with additional fire escape stairs, not shown) as well as for daylight and sunshine control, rain protection and acoustical absorption.
3) The care for the human scale, avoiding large monoliths.
Energy (¥ equals kWh) and building components
The construction must be low cost such as to limit the embodied energy.
The running costs must be limited such as to limit the daily consumed energy.
Reducing those costs reduces the environmental impact of the construction and of its use.
The aim to limit the construction cost leads to propose:
– no earth movements,
– a clean, dust free, noise free, fast construction process,
– every building component fully prefabricated and as light as possible.
Thus, and for example:
– screwed steel pile foundations,
– columns, truss beams, catways, stairs and vertical circulation structure out of steel,
– massive wood logs forming the structural floors and wall panels,
– all windows openable, in wood with ultra-clear vacuum glass,
– bamboo walking floors,
– all cabling and piping aerial and accessible,
– stainless or Corten steel sanitary equipment,
– recycled (+ historic) furniture and textile rewoven fabrics.
The aim to limit the running cost leads to propose:
– natural lighting where available, RGBV (red-green- blue-violet) LED (light emitting diode) where daylight is insufficient (the addition of the violet LED providing a wavelength spectrum equal to daylight),
– natural ventilation when T° ≥ 15°C, mechanical ventilation with heat recovering when T° ≤ 15°C,
– rainwater harvesting and storage,
– sun energy harvesting with redox batteries storage,
– wind flow control.
Thus, and for example:
– monitored mirror aluminium louvers perforated at 50 % (vertical on East and West façades, horizontal on North and South façades) placed outside. The catways provide daylight and sun protection inside, reflect daylight and sky views to the garden park, while protecting from fall as well as against intrusion,
– controllable air flows, enough for summer cross ventilation but limited enough to avoid winter cold drafts in the garden park,
– rainwater tanks at roof levels (located within the vertical circulation shafts) as well as at the lower service level to collect the garden park water; the water is used for the toilets as well as for the plantations,
– photovoltaic canopies above the upper building gardens with redox batteries,
– a geothermal installation for temporary summer air conditioning and winter heating,
– Macadam pavement for the roads and parking zone at level 0 (without any bituminous content).